PQP (Plasma-Quench-Polish) is a modern surface treatment for metal components that combines plasma hardening, quenching, and polishing to achieve extreme durability, hardness, and a smooth surface. This process is primarily used in the firearms, aerospace, and automotive industries as well as for high-stress components in airsoft. For example, it is applied to the metal bodies of Arcturus weapons, which you can purchase on our e-shop.
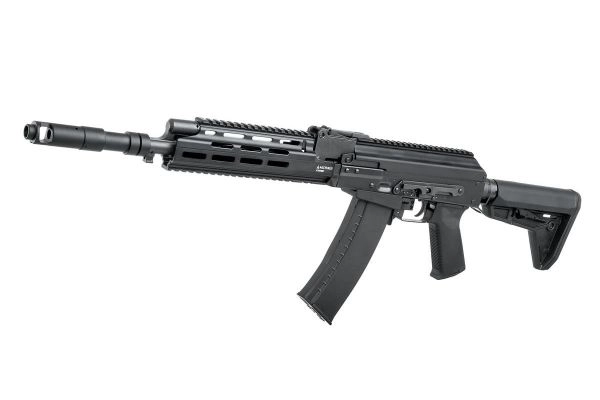
How does the PQP surface treatment work?
- Plasma nitriding: The surface is exposed to an ionized gas in a high-voltage electric field, leading to diffusion enrichment with carbon and nitrogen, which significantly increases hardness.
- Quenching: After hardening, the material is rapidly cooled to fix the hardened structure and enhance its resistance to wear.
- Polishing: The final stage involves fine polishing, which minimizes friction and improves the component’s visual appearance.
Advantages of PQP surface treatment:
- Extreme hardness: Surface hardness can reach up to 1200 HV (Vickers), comparable to titanium.
- High wear resistance: Extends the lifespan of components due to reduced friction and increased abrasion resistance.
- Corrosion protection: Plasma hardening reduces susceptibility to corrosion and chemical damage.
- Smooth surface: After polishing, the surface remains extremely smooth, improving mechanical properties.
- Increased thermal resistance: The surface retains its strength even at high operating temperatures.
Disadvantages of PQP surface treatment:
- Higher cost: The complex technological process increases production costs.
- Specific applications: Most commonly used for high-stress components (barrels, slides, pistons) but not suitable for all materials.